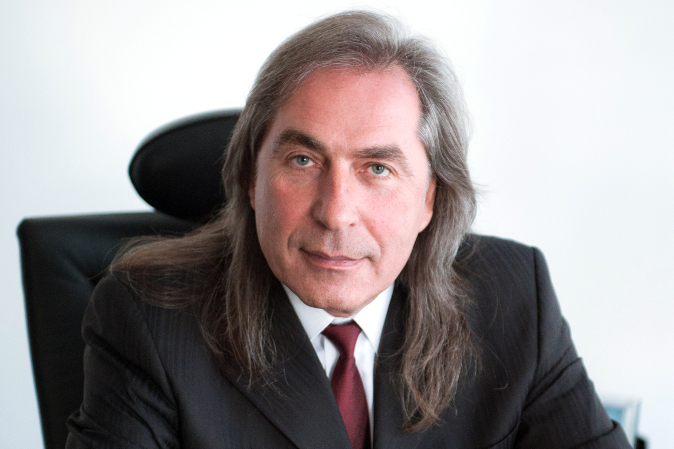
Передовые технологии в авторемонте или «вода» всему голова
В европейских странах использование более экологически чистых водорастворимых материалов регулируется на законодательном уровне. В России же экологические требования менее жесткие. В том числе и по этой причине базовые покрытия на водной основе в России распространены меньше, чем сольвентные. В компании «Тойота Центр Красноярск» (входит в ГК «Крепость») решили перейти на более прогрессивные материалы. Процесс оказался безболезненным, при этом производительность кузовного участка выросла на 20%. Подробнее об этом рассказывает директор производства холдинга Петр Сергеевич Варыгин
– Еще в 2009 году Вы перешли с сольвентных на водоразбавляемые покрытия. Почему приняли такое решение?
– Производственные площади не позволяли выполнять тот объем работ, который давал рынок. Наличие одной окрасочной камеры стало для нас своеобразным «бутылочным горлышком», и нам нужно было его расширить, то есть получить максимальную продуктивность от имеющихся ресурсов. По совету нашего партнера «Цветовое решение», официального поставщика ЛКМ Sikkens от AkzoNobel, мы обратили внимание на водорастворимые покрытия Sikkens Autowave.
– Чем они Вас заинтересовали?
– Массой преимуществ по отношению к сольвентной системе. Что касается разработки инновационных материалов и новых цветов, фокус внимания производителя направлен в первую очередь на водные материалы. Поэтому у нас есть уникальная возможность применять в работе самые передовые технологии и материалы. А это уже совершенно другие скорости и принципиально новые возможности. Производственный цикл окраски занимает меньше времени – экономия порядка 15 минут на деталь. Высокая укрывистость материалов и точность цветоподбора значительно экономят расход материалов. Кроме того, материалы на водной основе чаще прощают ошибки, что сокращает количество «перекрасов». Впрочем, их доля всегда была несущественной. Раньше – 10-15 на тысячу заездов, теперь – пять-шесть.
– Какие трудности возникли при переходе на новый вид материалов?
– Безусловно, опасения были. Необходимо было перейти на работу с водорастворимыми покрытиями Sikkens Autowave и LV лаками в кратчайшие сроки и без снижения текущего показателя производительности цеха. И, как показала практика, процесс для нас был безболезненным. Докупать оборудование не пришлось, так как мы изначально установили окрасочную камеру, предназначенную для работы с материалами на водной основе. Персонал обучили в Информационно-учебном центре AkzoNobel в Москве, а также локально – непосредственно на производстве во время выполнения работ по окраске и колеровке.
Примечательно, что технология нанесения водных материалов довольно схожа с технологией нанесения сольвента, что позволяет перейти на работу с водными материалами с минимальными потерями в эффективности, качестве и времени. При этом появилась возможность красить большее количество деталей «в стык» без необходимости разборки и окраски сопряженных элементов. Что в общей картине очень сказалось на эффективности процесса.
Единственное, с чем могли возникнуть сложности – это перебои поставок материалов в холодный сезон – ведь краска на водной основе чувствительна к низким температурам. Но, благодаря точному планированию нашего партнера «Цветовое решение», вопрос был решен очень просто. На основе статистики потребления материалов станции в зависимости от выработки был создан пятимесячный складской запас. Доставка осуществлялась к нам в специальных утепленных контейнерах. Поэтому техническая поддержка в переходе на новые материалы, пожалуй, сыграла важную роль.
– Насколько работа с водоразбавляемыми покрытиями изменила эффективность производства?
– Переход на новые материалы был частью принятых нами мер. Если говорить в целом, то представьте, на кузовном участке «Тойота Центр Красноярск» действует одна окрасочная камера, 4 поста подготовки, 13 кузовных постов. Работаем в одну смену. Средний показатель выработки аналогичных станций с одной окрасочной камерой по России составляет 3,5 тысячи нормочасов в месяц. Мы же можем производить 5,3-5,6 тысячи нормочасов.
– Какие решения дополнительно повлияли на повышение эффективности?
– К ним можно отнести бригадный метод работы, который для современных кузовных станций стал, скорее, исключением из привычной практики, но повысил производительность на 20%. Кроме того, стоит отметить автоматизированную систему учета и списания материалов, которую мы создавали с учетом потребностей нашей станции. АСУМ позволяет нормировать ЛКМ и не ЛКМ, контролировать текущий фактический расход и управлять складскими запасами. Результат – сокращение расходов ЛКМ и не ЛКМ, примерно на 30%.
Материал опубликован на правах информационного партнерства

0
27133
Другие статьи:
- 23 мая 2025
- Toyota Alphard отзывают для замены молдинга
- 3 апреля 2025
- На внедорожниках Toyota и Lexus заменят двигатель
- 17 марта 2025
- Бывший завод Toyota готовят к расконсервации
- 7 марта 2025
- В России отзывают 2,2 тысячи Toyota Highlander
- 3 февраля 2025
- Toyota осталась лидером в автопроме
- 16 сентября 2024
- Toyota Camry лидирует по спросу в своей категории
- 12 сентября 2024
- «Фреш» стал владельцем салона Toyota в Тюмени
- 3 июня 2024
- Росстандарт отзывает внедорожники Toyota и Lexus
- 7 мая 2024
- Бывший завод Toyota передали «Аурусу»
- 19 марта 2024
- Кузбасские центры Toyota и Lexus уйдут с молотка
Комментарии
Чтобы оставлять комментарии, необходимо авторизоваться на сайте