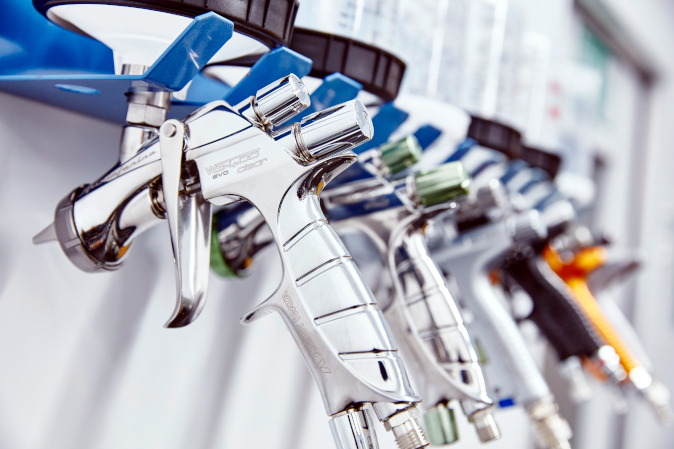
Быстрый аудит кузовного цеха: что можно узнать за 10 минут?
Как-то во время тренинга «Управление кузовным цехом: Sikkens BMT» ко мне обратился с вопросом один из участников – технический директор дилерского центра. Вопрос звучал примерно так: «Мы рассмотрели производственные факторы, влияющие на экономику, качество и эффективность, но для их проверки нужен специалист. Могу я сам как руководитель проверить что-то во время ежедневного короткого визита в цех?». Так появился «Чек-лист проверки руководителя»
Критерии, предъявленные к такому контрольному списку, звучали так:
– время проверки всех пунктов не должно превышать 10 минут;
– должны быть включены пункты, которые могут ежедневно меняться (т.е. не нужно задаваться вопросом: «Есть ли в МКЦ окрасочная камера?» и т.д.;
– для проверки не нужно быть специалистом, нужно просто указывать «что вижу / не вижу».
В результате этого вопроса родился «Чек-лист проверки руководителя», который существовал некоторое время в формате диаграммы Mind map, а затем был преобразован в интерактивный тест, который можно пройти на сайте AkzoNobelConsulting.ru
В этом материале я хочу рассказать, почему важно включить именно эти пункты в ежедневную проверку и поделиться своими наблюдениями, собранными во время аудитов за последние годы.
Охрана труда – на что обратить внимание
Начать стоит с вопросов охраны труда. Законодательство в этой области в России строгое, а ответственность всегда ложиться
Сергей Осипов, директор по бизнес-консалтингу «Акзо Нобель Автопокрытия»
на руководителя предприятия или соответствующего подразделения. Конечно, можно защитить себя юридически, если сотрудникам все, что нужно, предоставлено, все инструктажи проведены и все подписи в журналах поставлены.
Но еще лучше вовремя исключить на производстве самые опасные факторы.
Вот пример: почти в каждом кузовном цехе в России и за рубежом можно увидеть персонал, носящий обычные пластиковые тапочки вместо надлежащей рабочей обуви. Отговорки могут быть самые разные: и «обувь тяжелая», и «в ней жарко», и «в ней неудобно» и т.д. Но когда я вижу, что, например, подготовщик тащит в руках капот (естественно вертикально, острой кромкой вниз) и при этом он в тапочках с открытыми носками, мне становиться страшно. А если уронит себе на ногу? Это гарантированная производственная травма. Не даром рабочая обувь, положенная по регламенту, защищает от таких воздействий, а заодно и от паров растворителей, которые тяжелее воздуха и собираются у пола.
На основе подобных, наиболее частых нарушений появился раздел чек-листа по охране труда. В него вошли только видимые факторы, не требующие дополнительных проверок и измерений.
Расходы кузовного цеха
Другой популярный раздел вопросов руководителей – это затраты цеха. Понятно, что о затратах можно судить по отчетам и показателям, но причины лишних расходов, так сказать «денег на ветер», находятся внутри производства и вполне видны невооруженным взглядом.
Во время своих аудитов в МКЦ я часто вижу картину: окрасочная камера (ОСК) стоит включенной в режиме нанесения – воздух забирается снаружи и подогревается, двери при этом открыты, часть деталей уже внутри. Почему так происходит? Чаще всего потому, что маляр думал, все уже готово к следующему циклу, включил камеру, начал заносить детали. Вдруг выяснилось, что по одному из заказ-нарядов еще не готова краска или обнаружился дефект подготовки. Обычно в таком случае сотрудник не останавливает окрасочную камеру, а просто отходит и занимается другими делами. Порой такое непродуктивное ожидание длится более часа, а все это время ОСК сжигает топливо в самом энергоемком режиме. Хорошо еще, если ОСК работает на газе и на улице лето, а если не так? Другая причина подобного явления – это преднамеренное использование ОСК персоналом как отопительного прибора. Банально – в цехе холодно в начале смены. Открываем двери, включаем камеру и греемся! Дорого, зато эффективно…
Подобные пункты тоже были включены в проверку руководителя, и они легко и быстро выявляются путем наблюдения.
Продуктивность цеха
Производственные площади и оборудование стоят денег. Я часто вижу внутри кузовного цеха много машин, стоящих на рабочих постах без каких-либо действий с ними. Вот просто стоит машина, занимает пост как парковку часами, иногда даже полный день смены. При этом подготовка другого автомобиля идет где-то рядом в проходе. Почему так? Чаще всего – загнали на пост машину с несъемной деталью. Возможно, не все детали под замену уже готовы или циклы ОСК не спланированы, ведь для окраски несъемного элемента машину нужно загнать в камеру целиком. Вот и стоит этот автомобиль – ждет своей очереди или готовности, занимает при этом дорогостоящее место. А от начальника цеха при этом требуют выработку, ведь каждый нормочас на счету.
И это лишь один из факторов снижения эффективности производства. Такие факторы, самые простые, явно видимые, также вошли в чек-лист.
Подведем итог
Руководитель действительно может быстро проверить «здоровье своего производства» во время регулярного визита, даже за чашкой утреннего кофе. Набор пунктов проверки позволяет не растрачивать внимание, а сосредоточиться на главном. А после получения результатов можно подумать о новых правилах или целом плане по улучшению процессов в кузовном цехе.
Материал опубликован на правах информационного партнерства

0
22766
Другие статьи:
- 16 июня 2022
- Дилера оштрафовали за нарушение сроков ремонта на сумму, в 10 раз превышающую стоимость машины
- 18 ноября 2019
- Анонс номера «АвтоБизнесРевю» за ноябрь
- 17 января 2019
- Верховный суд заглянет в сервис
- 30 июня 2017
- «Росгосстрах»: 90% загрузки МКЦ дает страховщик
- 10 февраля 2016
- «Рольф» запускает центр кузовного ремонта
Комментарии
Чтобы оставлять комментарии, необходимо авторизоваться на сайте